Reverse Osmosis Chemicals
ALL INNOVATIONS
- Water Treatment Consultancy and Engineering Services
- AC4400 Electro Chemical Reactor
- Waste Water Recovery
- Clean Water Filtration
- Reverse Osmosis Systems
- Ultra Filtration Systems
- Sand Filters
- Softening Systems
- Process Water Analysis
- Cetamine
- Boiler Water
- Mechanical Filtration Consultancy Project and Engineering Services
- Iron and Steel Industry
- Wastewater Recycling Consultancy Engineering and Project Services
- Wastewater Analysis
- Cooling Treatment
- Power Plants
- Deposit Analysis
- Closed Circuit Water Treatment Chemicals
- Food and Beverage Industry
- Paper and Wood Industry
- Reverse Osmosis Chemicals
- Corrsave® 100
- Legionella Analysis
- Geothermal Industry
- Ultrasonic Thickness Measurement Analysis
- Dilurit® BC S
- Wastewater Treatment Chemicals
- Automotive Industry
- Drinking Water Treatment
- Membrane Autopsy Analysis
- Pool Water Treatment
- Chemical and Pharmaceutical Industry
- DReeM Polymer™
- Dust Collectors
- Refinery and Petrochemical
- Tunnel and Mining
- HydroBio Advance
- Geothermal
- KuriLoc Kit
- Manufacturing Industry
- Kuriverter™ IK-110
- S.sensing CS
- S.Sensing Matrix System
- RC Box Applications (RC Membrane Repair)
- Online Automation
- Electro Chemical Reactor
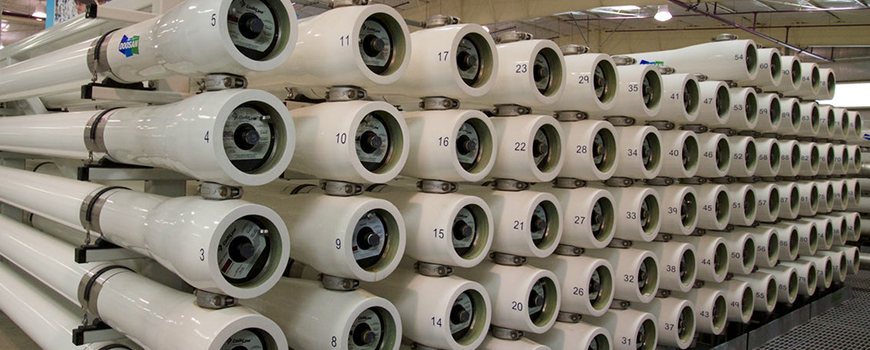
Membrane Conditioning with Reverse Osmosis Systems.
Membrane units are now widely used in water treatment with pre-treatment and have become one of the most important technologies in high purity water production. However, these units have a high risk of lime and deposit formation and contamination, so membrane technology often requires maintenance and downtime, and restrictions such as high operating costs may occur. Our conditioning programs are specifically designed for reverse osmosis, ultra and nanofiltration, also provide preventive control against scale and sediment formation and contamination in membrane units. Our main goal is to ensure that these facilities are environmentally friendly and economical to operate. In addition to efficient use of energy, particular attention is paid to the protection of valuable water resources. Kurita has developed an efficient and effective conditioning concept to achieve optimal cost-effective operation and maximum operational reliability in the plants.
- Membrane units are used in various industries:
- Surface technologies (cutting oils, processing oils, emulsions, cataphoresis bath, phosphate bath, paint, cleaning bath)
- Desalination of sea water
- Waste water
- Boiler feed water preparation
- Biotechnology
- Pharmaceutical industry
What kind of products does Kurita offer?
- Kuriverter ™ / Osmotech®: Cleaner, antiscalant and dispersant series for membrane conditioning
- Kuriverter ™ IK-110: Biofilm removal
- Kuriverter ™ RC: Concept for renewing damaged membranes
- Ferrocid®: Biocide * series compatible with membranes
Antiscalants.
Regular monitoring of the plant's operational performance and regular maintenance is essential for trouble-free operation. More importantly, the membranes must be protected against lime and sediment formation and contamination in order to maximize the life and prevent unnecessary and unwanted downtime.We select the most suitable antiscalants for each application and feed water quality.
Kurita antiscalants have an excellent inhibitory effect for a wide range of deposit types:
- Colloids and suspended solids
- Iron and manganese
- Calcium carbonate
- Calcium sulfate
- Strontium sulfate
- Barium sulfate
- Silicate
Our product portfolio also includes NSF certified antiscalants.
Biocides.
Biological, organic and inorganic contaminants in the feed water accumulate on the membrane surface. Accumulation on the surface of the membrane caused by impurities in feed water is generally called "fouling". The deposits formed by adsorption of microorganisms on the surface of the membrane are called "biofouling". Biological contamination is a problem that needs to be paid attention because microorganisms can reproduce at an exponential rate and risk to completely cover the membrane surface. As a result, the efficiency of the plant is significantly reduced, irreparable damages on the membrane can occur.Addition of daily biocide and biological contamination control products are necessary and recommended to effectively prevent the biofouling process. Kurita has developed special biocides * to contribute to the economic operation of reverse osmosis systems. The most outstanding advantages of our technology:
- Low dosage
- Removal of existing biofilm
- Prevention of microorganism resistance
Preconditioning.
The stress load of the plant should be reduced as much as possible by effective pre-conditioning of the feed water. Depending on the raw water quality, pre-treatment processes such as coagulation, flocculation, sedimentation and filtration can be used.Kurita offers a rich and deep expertise in these conditioning stages as well as advanced and innovative products designed specifically. The right products can be selected by performing laboratory tests with various analytical methods such as SDI measurements.
Cleaning.
Effective preconditioning is a fundamental requirement for the proper operation of reverse osmosis plants. However, preconditioning cannot completely prevent contamination, scale and sediment formation, which reduces the performance of the membranes. This significantly reduces the quality of the water produced, while significantly increasing the energy requirement of the plant. Colloidal and microbiological deposits as well as the formation of deposits originated by metal hydroxides are the basis of this loss of performance. In addition, CaCO3, CaSO4, SiO2, BaSO4 and CaF2 deposits also reduce the efficieny of product water.Therefore, it is necessary to clean the membranes regularly. Special requirements necessitate tailor-made solutions for the right cleaning process. Kurita conducts several preliminary investigations to develop an accurate cleaning procedure. The following points are of particular importance:
- Membrane autopsy
- Performance tests
- Water analysis
- Purification tests
- Deposit analysis
Consultancy and Service.
A good understanding of the design and operation of RO (reverse osmosis) systems forms the basis of a successful conditioning concept. In accordance with this principle, the following investigations are carried out in our scientific research laboratories:
- Deposit and water analysis
- Membrane autopsy
- Horizontal membrane tests
- Cleaning tests
- Microscopic investigations
- Surface analysis
With these comprehensive preliminary investigations, it is possible to select the most suitable biocides, antiscalants and cleaning chemicals for the plant's economic and environmentally friendly operation.
* Caution: Biocides should be used with due regard to safety precautions. The label and product information must be read before using.
With our experience and expert staff, we develop solutions tailored to your needs. We are also glad to offer our business-specific consulting services.